Infrastructure
Manufacturing Process
Manufacturing process starts with Wire Drawing The Copper or Aluminium wire rods drawn on high speed Rod break down Machine. Poly Crystalline Diamond Dies are used for drawing, which ensures the diameter of drawn wire as maintained within the tolerance limit.
For flexible / stranded conductor, fine wire drawing is carried out on high speed fine wire drawing machines. These are fully automatic machines with on-line resistance annealing system, which ensures uniform softness and flexibility of wires through out the length of the spool.
The fine drawn wires undergo bunching operations on high speed bunching machines ensuring even twisting..
The Copper or Aluminium drawn wires are stranded on tubular stranding machines to form conductor. (Conductor Stranding).
Insulation of building wire and Industrial wires is carried out on high speed twin head Extrusion System with Skin, stripes and tracer colouring system. The extrusion for XLPE and PVC insulated Power and Control Cables is carried out on specially designed extruder lines fitted with diameter controllers, on line spark tester and inkjet printing.
Before laying up, the XLPE insulated cores are steam cured under standard conditions. The cores are then laid up on planetary laying up machines and thermoplastic tape is wrapped over the laid up core.
The insulated core for instrumentation and signal cables are twisted to form a pair and shielded with Polyester coated Aluminium tape. In certain cases, the screening is carried out on imported high speed braiding machine with tinned/bare copper wire. (Pairing and screening )
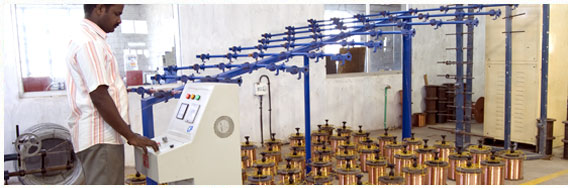 |
Laid up cores are then armoured with Galvanised round steel wire or flat strip. Armouring is carried out on machines with Synchronous drive system ensuring smooth and more than 95% coverage.
Outer sheathing is carried out on extrusion lines with online diameter controllers, on-line spark tester and inkjet printing machines.
|